
Ural Steel is the optimal combination of rich experience, new technologies, team of professionals and aspiration for leadership.
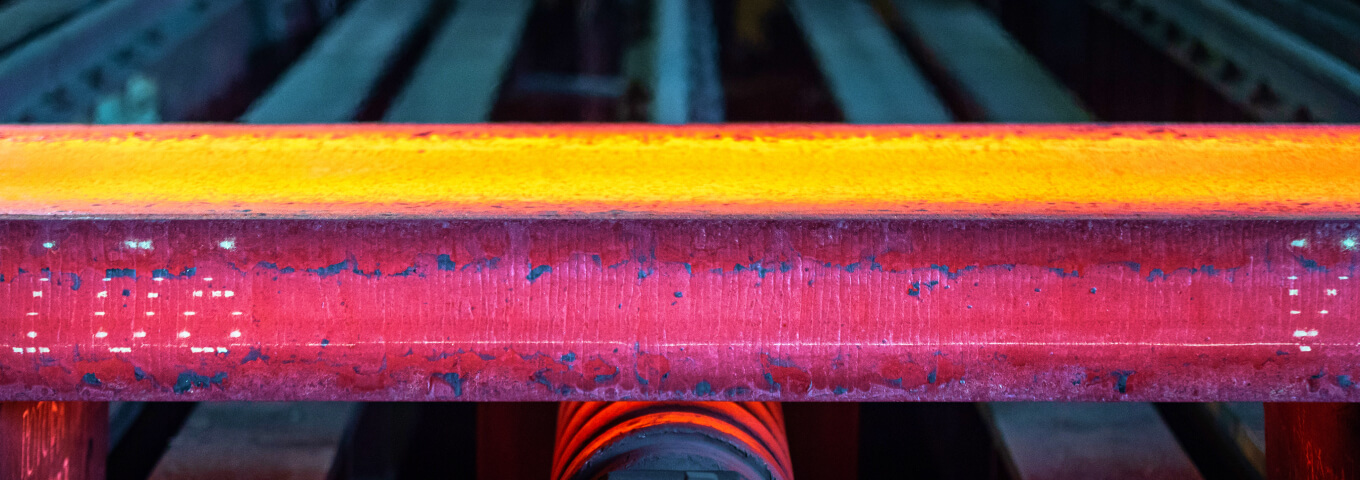
Production
It includes the following main process stages: sinter,
coke and by product, blast furnace, steelmaking,
plate rolling production. Company is developing Foundry Plant,
Tube Rolling Mill is being put into operation and construction
of Wheel Rolling Mill is planned.
-
0
million tons per
year sinter -
0
million tons per
year coke -
0
million tons per year
cast iron -
0
million tons per
year steel -
8 9 8 0 8 0
thousand tons per year
rolled products
-
Productive Sinter Plant
180 million tons +
of sinter
from startup in 1963(comparable to the weight of half of the Great Wall of China)
2.7 million tons +
of sinter
per year(with iron content of 56.1% with a basicity of 1.57)
Production equipment of the Sinter Plant:
Sintering Mix Preparation Area
- three tippler for unloading raw materials from open-top-wagon with a capacity of 500 tons per hour each,
- four hammer crushers for crushing limestone,
- five four-roll crushers for crushing fuel,
- conveyor kiln for lime production.
Sintering Area
- four Sinter Machines for mix sintering with a complex of equipment with a capacity of up to 110 tons per hour each,
- four pan coolers for sinter.
-
Multifunctional Coke and By-product Production
140 million tons+
produced
since 1950(the weight of Yamantau (1640 m), the highest mountain in the Southern Urals)
1.5 million tons+
of coke
annually(foundry and metallurgical coke, coke nut and coke fines, by-products: coal tar, ammonium sulfate and benzene)
Main equipment of Coke and By-product Plant:
Coal Preparation Plant with Areas
- Tipplers No.1, 2 for coal unloading,
- Open warehouse for coal storage,
- Dosing department for coal preparation for coking;
Coke Plant with Areas
- Coke Oven Batteries No. 1, 3, 4 for coke production,
- Coke Oven Battery No. 6 for coke production,
- Coke Screening Plant No. 1, 2 for coke screening by size - metallurgical coke for Blast Furnace Plant, nut and fines for third-party consumers;
By-product Recovery Plant with Areas
- Coke oven gas primary cooling department, condensation for tar production,
- Sulphate department for the production of ammonium sulphate,
- Benzene department for benzene production,
- Biochemical water treatment plant area.
-
Efficient Blast Furnace Plant
160 million tons +
since the first Blast Furnace started up on March 5, 1955.
(this amount of metal could be used to build 26 pyramids of Cheops)
2.7 million tons +
of cast iron per year
(high quality basic pig iron and basic pig iron of ordinary grades)
1.4 million tons +
of commercial pig iron per year
Main equipment of the Blast Furnace Plant:
- three Blast Furnaces BF-2, 3 and 4 with useful volumes of 1232, 1648 and 2015 m3,
- Casting Machines No.1-4 with capacity of 350 thousand tons of basic pig iron per year each,
- Casting Machine No.5 with capacity of 409,5 thousand tons of basic pig iron per year,
- Slag Processing Plant with a capacity of 1.1 million tons of granulated slag per year.
-
Technological Steelmaking Plant
40 million tons +
of electric arc furnace steel over the years of the plant's operation since 1982
(it would be enough to make railroad rails to connect all continents of the planet)
1.8 million tons +
of steel per year
800 thousand tons +
of continuous cast billets
per year.(190x1200, 220x1200 and 270x1200 mm billets for rolled product; round wheel billets with diameter of 455 mm, 330x300 mm rectangular rail billets)
Main equipment of the Steelmaking Plant:
- Two unique 120-ton Flexible Modular Furnaces can operate both in electric arc melting mode and can melt steel using basic oxygen process without electrodes and electricity consumption (FMF technology),
- Two two-position Ladle Furnaces for desulfurization and steel quality improvement,
- Vacuum Degasser to practically remove hydrogen from the steel,
- Induction Heating Furnace to maintain an optimal temperature range for plastic deformation of the metal;
- Single-strand slab Continuous Casting Machine with cross-sections of 190, 220, 270 x 1240 mm,
- Four-strand combined Continuous Casting Machine for casting rectangular blooms of 300 x 330 mm in cross-section and rounds of 455, 540 and 600 mm in diameter.
-
Unique Plate Rolling Production
60 million tons
of rolled products over the years of 2800 Mill operation since 1960.
(it would be enough to lay plates and wrap the Earth five times along the equator)
900 thousand tons
of rolled plates per year
320 thousand tons +
heat-treated rolled products per year
500 thousand tons +
strips per year
Main equipment of Plate Rolling Mill-1:
2800 Plate Rolling Mill
- Four Reheating Furnaces (two main furnaces are equipped with modern Automated Control System (ACS) for the reheating process, as well as impact free slab discharging machine),
- Three High-Pressure Descalers for maximum descaling during rolling,
- Two-high roughing stand with rolling force 32500 kN,
- Four-high finishing stand with rolling force of 60000 kN,
- Laminar-type Accelerated Cooling Unit equipped with a self-learning cooling model,
- Eleven-roller Hot Straightening Machine,
- Shears for longitudinal and transverse cutting of rolled products,
- Metal Inspection and Grinding Area,
- Two modern Ultrasonic Testing Units;
Heat Treatment Area
- Four Roller-Hearth Heat Treatment Furnaces (one of them is equipped with modern ACS system) up to 30 thousand tons of rolled products per month,
- State-of-the-art Roller-Type Quenching Machine, which allows to ensure uniformity of mechanical properties of rolled products after heat treatment of plates up to 12 m long,
- Quenching Press for quenching shorter plates,
- Three Plate Leveling Machines,
- Cooling bed to ensure cooling in the air after normalization,
- Metal Inspection and Grinding Area.
-
Universal Foundry
4 million tons
of castings produced since 1958.
(it would be enough to cast 20 thousand equivalents of the world's largest Tsar Bell)
10 thousand tons
of small and large-size castings per year
(of required configurations and dimensions, chemical and mechanical properties)
Main equipment of the Foundry Plant
Foundry Area (manufacturing of products from 0.01 to 6 tons)
- Melting complex IST-2,0/1,0 with working volume of 1 ton,
- Regeneration line of used molding sand,
- Electric Furnace EAF 6 H 1 with working volume of 6 tons,
- Electric Furnace for non-ferrous castings SMB 0.6341 with working volume of 500 kg,
- Continuous Mixer SNDVA-2-10 for preparation of molding cold hardening mixture, up to 10 tons/hour,
- SPARTAN 320 Continuous Mixer with a capacity of 20 tons/hour,
- Five-axis CNC machining center with cabinet protection mod. “ORSISXL” (E9-2030) n for plane and profile machining;
Large-size Casting Area (manufacturing of products from 3 to 83 tons)
- Continuous mixer model MV30V510 with a capacity of 30 tons/hour,
- STD 5000*6500 shake-out grid for used molding sand,
- Shot blasting unit KOM-5100x3900 for cleaning of products from molding sand adherence,
- Self-propelled car with a carrying capacity of 100 tons for moving the molded tooling,
- ventilation system of the molding sand discharging area.